MARKET AND SEGMENTS
The global waste heat into electricity conversion market is still virtually untapped EACH country in the world has thousants of potential customers , in total worth billions ?
SEGMENTS FOR EACH COUNTRY
- Biomass plants Installations
- Biogas plants Installations
- Diesel /gas engines generators exhausts
- Metal Industry
- Cement industry
- Glass industry
- Ceramic industry
- Paper industry
- Non ferrous furnaces
- Refineries
- Agriculture Green houses
- Food processing industry
- Geothermal solutions
- Leisure heated swimming pools
- Sites isolated from grid power (f.i. marine ships, remote locations, islands etc)
- Waste incineration (waste to energy)
- CSP (Concentrated Solar Power) projects
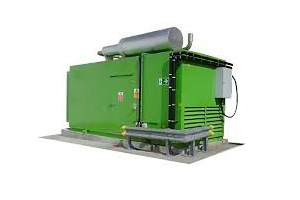
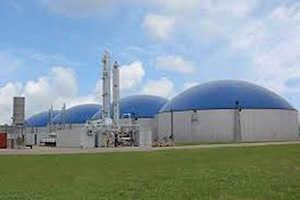
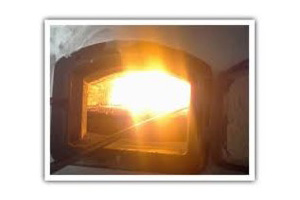
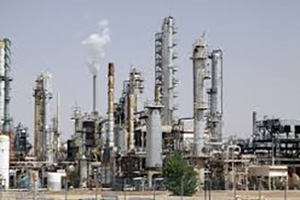
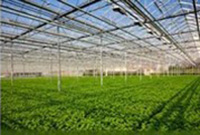
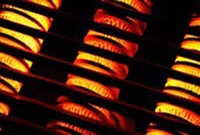
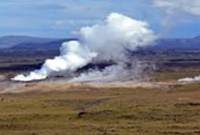
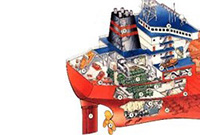
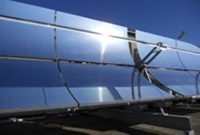
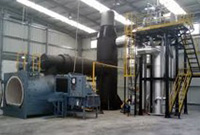
COMPETITION
In relation to the huge potential market, the competition is very limited and for some temperature capacity segments even not present at all!
Termo2Power has a very wide assortment range using varioous type of ?expander turbine technologies
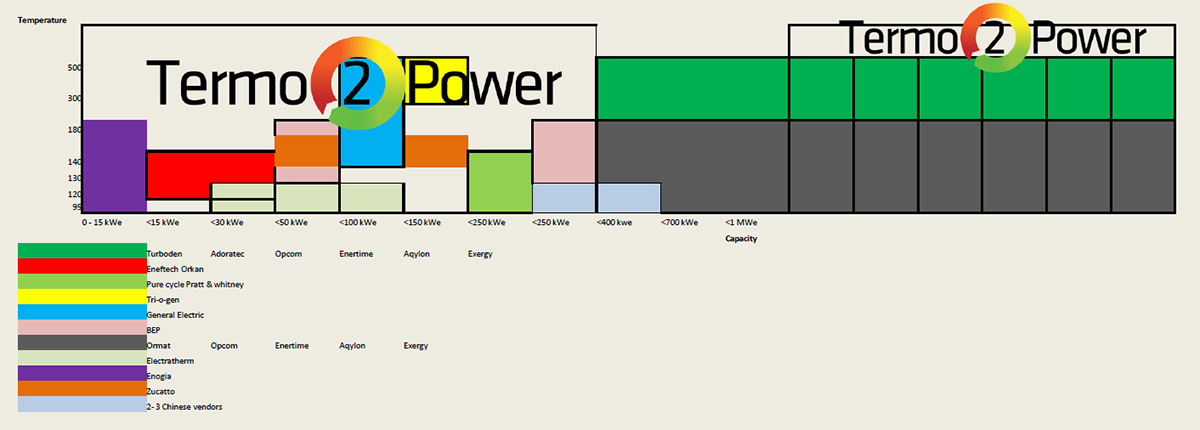
- World wide there are less than 20 companies offering heat to power solutions.
- Each competitor has a rather narrow temperature and capacity range, so for a given temperature range capacity there are only between 0 5 companies competing
- Given the amount of customers and limited offer it is a clear SELLERS market
Technical applications
?Waste? heat source | Systeem working fluids options | Cooling requirements Efficiencies & Applications |
---|---|---|
Liquid 95?C – 130?C | Methanol/R245fa | < 20?C Water
|
Liquid 120?C – 220?C Gas 250?C – 450?C |
Ethanol – SES 36 Cyclopentane | < 40?C Water/cooling tower
|
Liquid 220?C – 320?C Gas 370 ?C ? 850 ?C |
Siloxanes MM/MDM STEAM CYCLE |
< 100?C Water/cooling tower
|
The schedule of technical applications show that when we have low temperature heat source like 95 C – 120 C the ORC working fluid can be R245fa , but it implicates that because of its boiling point of 14,7 C we need cooling water of 12 C (or lower) to have a reasonable kWe efficiency of max 7% ? 9%.
When there is no cooling water of that temperature available the efficiency will be lower as to the point of where is no nett electricity production at all, because there is not only power consumption from the ORC systempump ? automatics, but also from hot and cold side circulation pumps/fans.
In case we have high temperature liquids or fluegas higher than 410 C it is possible to implement a steam cycle system in stead of a high temperature siloxane driven ORC. Only with this level of heat sources it is possible to have full co-generation applications for heating or drying.
Termo2Power prefers steam cycle applications because the working fluid ( Water = R718 ) is cheaper and more ecological than refrigerants or siloxanes. In addition the steam system does not need any expander lubrication injection- separation system, what makes the system easier- cheaper.
Also for heat recovery from (bio)gas-diesel combustion engines exhausts the steam cycle is preferred because otherwise there is need of an intermediate heat exchanger and a thermal oil loop before it can heat up an ORC working fluid like Solkatherm SES36.